3 Improvement measures
3.1 improve the accuracy of side guide plate equipment
Rectification of measurement problems found in the system, back side guide of the bell mouth and parallel to the period of transition place there is a big problem of the steps taken two measures, one is parallel to the side guide segment lining board cut thin 15 mm, 2 it is to push the bell mouth whole to run way among the 17 mm, big big reduce the height of the steps, improve the state of strip head into steel, drop we were among the strip local compression of the risk of collapse.
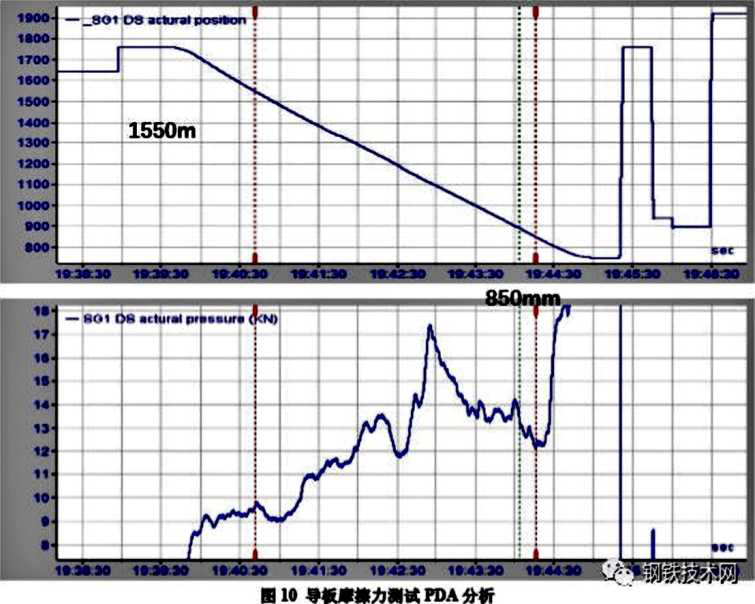
3.2 reduce static friction force of side guide plate
According to side guide friction problem, the factory repair, overhaul guide when ontology to replace copper skateboard, pin shaft, sets, gear, rack, eliminate clearance, more in equipment after the evaluation of static friction force decreased from 12 kn to 7 kn, and daily maintenance, working in the issued standard every day preview of 1 # SG drive side action mechanism, improve the frictional force, in the long run, will serve two hot side guide structure, the sliding friction into rolling friction can significantly reduce the static friction force, thereby greatly reducing the pressure of side guide target and fundamentally solve the problem of surface litter volume.
3.3 sectional pressure control of side guide plate
Under the existing conditions, it is necessary to not only ensure the roll shape, but also reduce the surface and groove rolls, optimize the control strategy of the side guide plate, and develop the pressure control method of the side guide plate sections. The pressure can be reduced to Y% of the target pressure after the drum bites the steel for X seconds. Both X and Y are adjustable parameters, which can be adjusted according to the actual situation.
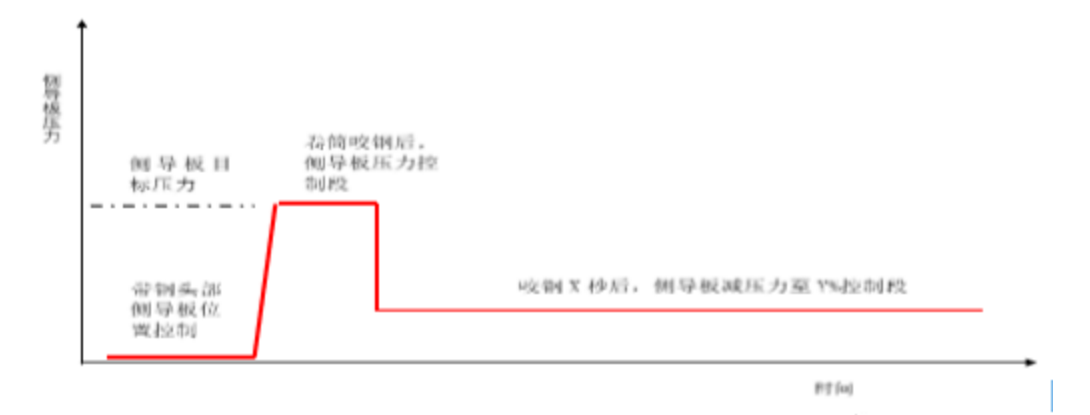
4 Implementation Effect
After the implementation of the above measures, bread rolls from 500 tons per month to less than 100 tons, a significant effect.5 conclusion
(1) the excessive suwa pressure on the winding side caused the strip edge to collapse and roll up, which was the direct cause of the surface roll;
(2) in terms of equipment accuracy, the step between the side flared mouth and the parallel section transition is too large, resulting in the head hitting when entering the steel, resulting in the skew. In the pressure link, the strip steel is locally compressed, and the edge is strongly compressed. This problem is eliminated by rectifying the equipment;
(3) the sudden static friction force on the winding side causes the target pressure to be large. By making the sudie uniform speed movement, the friction force can be measured indirectly and effectively. The static friction force can be reduced by replacing the gear, rack, copper slider and daily oil drilling.
Under the premise of ensuring the coil shape, the control strategy of pressure section can mitigate the damage of the side suwa to the edge of the strip.