Comparison of properties of different coatings
Painter Type | Hardness | Bending | Anticorrosion | Weatherability | Cost | Paint Thickness/um |
PE | Good | Ok | Ok | Ok | Good | 20 |
Acrylic Resin | Good | Normal | Ok | Ok | Bad | 20 |
SMP | Ok | Normal | Ok | Good | Ok | 20 |
PVC Plastisol | Normal | Good | Good | Ok | Bad | 200 |
PVDF | Normal | Good | Good | Ok | Bad | 25 |
HDP | Ok | Good | Ok | Good | Ok | 20 |
The two most important factors in the selection of primers are,
One is the adhesion of the primer and the finish substrate,
The second is that the primer provides most of the corrosion resistance of the coating.
From this point of view, epoxy is the only choice.
If considering flexibility, considering uv resistance, can also choose polyurethane primer.
For the back coating, the most correct choice is to choose a two-layer structure if the painted steel plate is used in a single layer.
Namely a back primer, a back finish.The primer is the same as the front, and the top coat is a layer of polyester in a light color (such as white).
If the painted steel plate is in composite or sandwich condition, an epoxy resin with excellent adhesion and corrosion resistance on the back will do.
Coating Gloss Selection
Effect of coating thickness on corrosion resistance of color coated plate
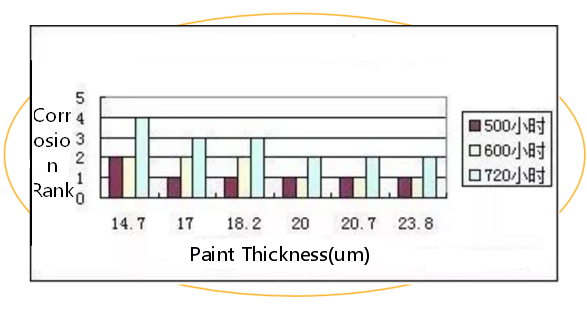
Gloss does not belong to the coating performance index, and color, it is just a characterization.In fact, coatings (coatings) are easier to achieve high gloss.
However, the high reflectivity of the high-gloss surface to sunlight during the day will cause light pollution (many of them do not use glass curtain wall now because of light pollution). In addition, the friction coefficient of the high-gloss surface is small, which is easy to slip.Color coated steel plate in the outdoor use of aging is the loss of light, if need to repair, between the new and old steel plate is easy to distinguish, resulting in poor appearance;
If the back paint is high gloss indoor lighting easy to produce halo and cause visual fatigue.Therefore, under normal circumstances, the color coated steel plate used in the construction of medium and low gloss (30-40 degrees).
Coating thickness selection
At the micro level, the coating is porous tissue.Water in the air and corrosive media (chloride ions, etc.) will invade through the weak part of the coating, causing submembrane corrosion, which causes the coating to bubble and flake.
In addition, secondary coatings are denser than primary coatings, even with the same coating thickness.According to foreign reports and related corrosion test results, the front coating of more than 20 um can effectively prevent the invasion of corrosive medium,
Due to the different anti-corrosion mechanism of primers and topcoats, the total film thickness shall be specified, and the thickness of primers (5um) and topcoats (15um) shall be required respectively. Only in this way, the corrosion resistance of different parts of painted steel plates can be ensured to be balanced.
PVDF products require a thicker film.Because to provide a longer life guarantee.The requirements for the back coat depend on the use, the sandwich plate only requires a coat of adhesive primer.The formed steel plate because of indoor corrosion environment therefore also requires two coating.Thickness at least 10um.
Coating Color Selection
The choice of color is mainly to consider the matching with the surrounding environment and the owner’s interests, but from the perspective of the use of technology to speak light color paint pigment selection,
Can choose inorganic coating with superior durability (such as titanium dioxide, etc.), and the thermal reflection ability of coating is strong (the reflection coefficient reaches T tone of dark coating) the temperature of the coating itself in summer is relatively low, which is beneficial to the extension of coating life.
In addition, even if the coating color or powder, light color coating film changes after the contrast with the original color is small, the impact on the appearance is not big.
And dark color (especially more bright-coloured color) use organic color is in the majority, encounter ultraviolet radiation to fade easily, the shortest 3 months change color.
According to relevant experimental data, in summer, when the outside temperature at noon is the highest, the white surface is 10 degrees lower than the blue surface temperature, 19 degrees lower than the black surface.
Different colors reflect different amounts of sunlight.The following table lists the reflectivity of different colors
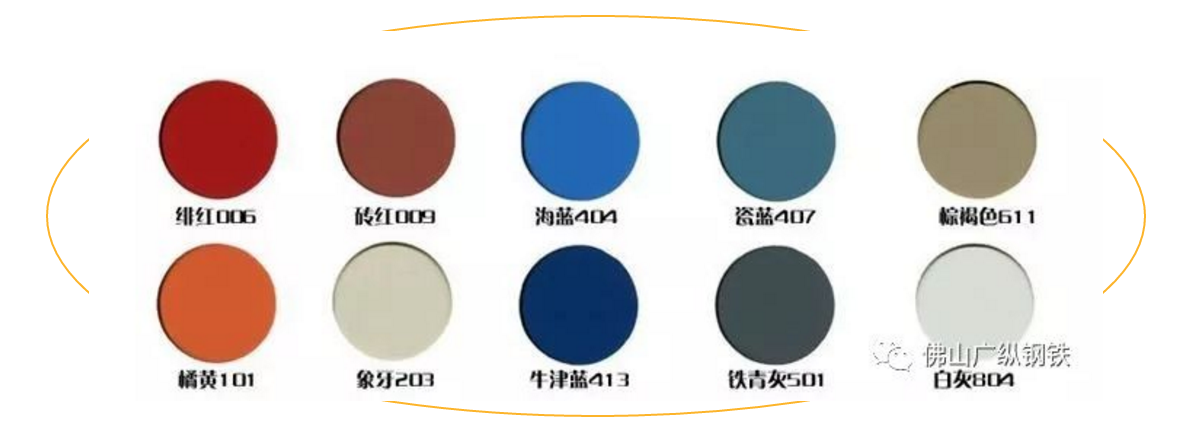
Color reflectivity reflection effect
For color coated steel plate, the thermal expansion rate of coating and steel plate is usually different, especially the linear expansion coefficient of metal substrate and organic coating is quite different, when the ambient temperature changes, the substrate and coating interface will occur expansion or contraction stress, if not properly released will occur coating cracking.
Baosteel has done the same coating variety in hainan, the same coating supplier, different colors of the 8 years of exposure test, the results also confirmed the light color coating color change is small.
Colour | Original Luster | Real Luster | Chromatism | Original Thickness | Real Thickness | Dusting |
White | 35% | 3% | 1.49 | 24 | 20 | 2 |
Red | 45% | 3% | 2.48 | 24 | 20 | 2 |
Light Yellow | 26% | 2% | 1.26 | 24 | 17 | 2 |
Green | 41% | 2% | 3.43 | 24 | 17 | 2 |
Blue | 41% | 2% | 4.95 | 24 | 17 | 2 |